De la anterior publicación relacionada con la captura de carbono se puede concluir que será una tecnología fundamental en el cumplimiento de los objetivos climáticos, siendo una pieza clave en el puzzle de la producción de compuestos renovables de alto valor añadido como el metanol o el SAF (keroseno sintético). De esta manera, para un desarrollo satisfactorio de la tecnología, es necesario conocer las implicaciones que tiene tanto en términos económicos (CAPEX y OPEX) como técnicos. De esta manera, uno se puede preguntar:
- ¿Cómo afectan las impurezas al proceso?
- ¿Qué costes implica una planta de captura? ¿Qué costes de CO2 implica?
- ¿A mayores de la inversión inicial, qué otros gastos acarrean este tipo de instalaciones (energía, mantenimientos, materias primas auxiliares…)?
- ¿Cómo se acopla una instalación de captura con una planta de combustibles renovables?
- ¿Qué implicaciones puede tener una planta de captura en un proceso existente?
En este artículo de AtlantHy Academy, abordaremos todos estos aspectos y responderemos a las preguntas basándonos en el conocimiento que hemos ido adquiriendo durante el desarrollo de este tipo de proyectos.
Impurezas procedentes del foco de emisión
Dependiendo de la fuente de emisión del dióxido de carbono, el gas de escape puede tener mayor o menor cantidad de impurezas, principalmente partículas, compuestos de azufre y de nitrógeno. La presencia de estos contaminantes puede implicar problemas en la operación nominal de las plantas, desde daño a equipos mecánicos (impacto de partículas) como formación de productos de degradación de los disolventes químicos por reacciones químicas entre las aminas y los compuestos de nitrógeno y azufre. En el caso de los productos de degradación, son de vital importancia dado que pueden resultar corrosivos para los aceros y terminar causando pérdida de contención en las unidades de proceso.
Para evitar estos fenómenos que afectan a la operación de la planta y que pueden implicar paradas inesperadas o una menor eficiencia, se debe dimensionar un pretratamiento adecuado del gas de escape antes de entrar a la planta de captura. En el caso de las aminas, este pretratamiento está formado principalmente por etapas de eliminación de partículas y etapas de eliminación de azufre y óxidos de nitrógeno empleando materias primas auxiliares como el hidróxido de sodio. En el caso de otras tecnologías como la criogenia, la etapa previa de eliminación de compuestos de azufre y nitrógeno puede ser prescindible, ya que el proceso no es tan sensible a estas impurezas, pudiendo eliminarse fácilmente por medio de las diferencias en las temperaturas de ebullición de los contaminantes y el CO2.

Ilustración 1. Scrubber para la eliminación de compuestos contaminantes presentes en el gas de escape.
En lo relativo a la presencia de partículas, pueden emplearse un sistema basado en filtros de mangas que aseguren que no se introducen sólidos en las conducciones de la planta de captura, asegurando la integridad de los equipos mecánicos y reduciendo la probabilidad de que surjan problemas en la operación.
Costes de inversión y del CO2 producido
Las plantas de captura son plantas muy similares a las plantas químicas convencionales, pues están formadas por unidades ampliamente conocidas en la industria como columnas de separación y absorción, equipos de flujo de fluidos y gases, tanques de almacenamiento y equipos de intercambio de calor y refrigeración. Debido a que los equipos empleados no son novedosos, sus costes son muy similares a los que llevan empleándose en la industria durante décadas.
En cuanto a los parámetros que más afectan a los costes de este tipo de plantas, principalmente se destacan la concentración del dióxido de carbono, pues cuanto mayor sea el valor de concentración, más económico será el proceso de captura al requerir de equipos más pequeños y, por lo tanto, menos costosos, y el tipo de tecnología empleada (aminas, carbonatos, criogenia…).
Por otro lado, otro factor fundamental es el conocido efecto de la economía de escala, pues los equipos empleados no aumentan su coste de manera proporcional a la escala, si no que siguen una función exponencial que hace que los proyectos más grandes logren costes de inversión más competitivos que los pequeños y, por lo tanto, puedan producir el dióxido de carbono a menor coste (la famosa regla del six tenth).
En cuanto a los gastos operacionales, están marcados principalmente por la elevada necesidad de energía térmica, de forma que este tipo de energía es la que marca los gastos operacionales de este tipo de plantas a lo largo de toda su vida útil.
A modo de orientación, una planta de captura con capacidad de 100.000 t CO2/año basada en aminas y empleada en una corriente de gas de escape con una concentración del 9%vol CO2, podría implicar una inversión de entre 40 – 50 M€.
A partir de los costes de inversión que se estiman para este tipo de plantas, se pueden obtener valores orientativos para el coste del CO2 producido en función de la concentración del foco de emisión y la magnitud del flujo. De esta manera, una estimación de los costes esperados del dióxido de carbono en función del caso específico se aporta en la siguiente ilustración.
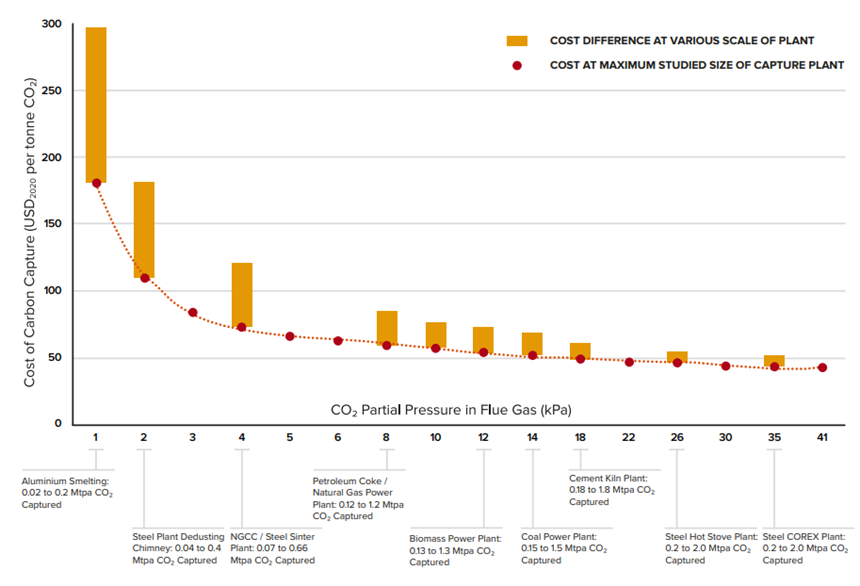
Ilustración 2. Costes de la captura de CO2 atendiendo al foco y la magnitud del flujo de gas de escape. Fuente: (Global CCUS Institute, 2021).
Consumos energéticos y de materias primas auxiliares en las plantas de captura
Para lograr la separación del dióxido de carbono de la corriente de gas de escape, se requiere, en función de la tecnología, de un aporte de energía eléctrica y/o térmica, los cuales deberán ser de origen renovable o poseer una intensidad de carbono baja. Esta necesidad de que los inputs energéticos sean renovables se debe a que el dióxido de carbono, aunque se capture y no se emita directamente, tendrá una huella de carbono asociada tanto a su origen como al proceso de captura en el que se obtiene en su forma pura. Por ello, esa intensidad de carbono se trasladará al producto final que se obtenga (SAF, metanol…) y puede implicar que el RFNBO obtenido no cumpla con lo estipulado en la RED III con respecto a la reducción de emisiones de gases de efecto invernadero (GEI).
Consumos eléctricos
En lo relativo a consumos eléctricos, estos se deben principalmente a los equipos de flujo de fluidos como las bombas de recirculación de aminas en la tecnología de absorción, soplantes para contrarrestar la caída de presión existente en las columnas de absorción y desorción del CO2 o para el empleo de compresores y equipos de refrigeración en el caso de la tecnología de criogenia. En cuanto a los valores específicos, estos varían entre 50 kWh/t CO2 para el caso de las aminas hasta 350 kWh/t CO2 para la captura basada en tecnología de criogenia.
A mayores de estos consumos, en casos en los que se capture el dióxido de carbono con tecnologías diferentes a la criogenia y el consumidor se ubique en un punto lejano al de la captura, puede ser necesaria la instalación de un sistema de licuefacción que permita el transporte de la molécula de manera sencilla mediante camión e incluso barco (transporte internacional). En estos casos, el consumo energético de la planta aumentaría en el orden de 210 – 260 kWh/t CO2 para poder cambiar la fase del dióxido de carbono producido de gas a líquido.
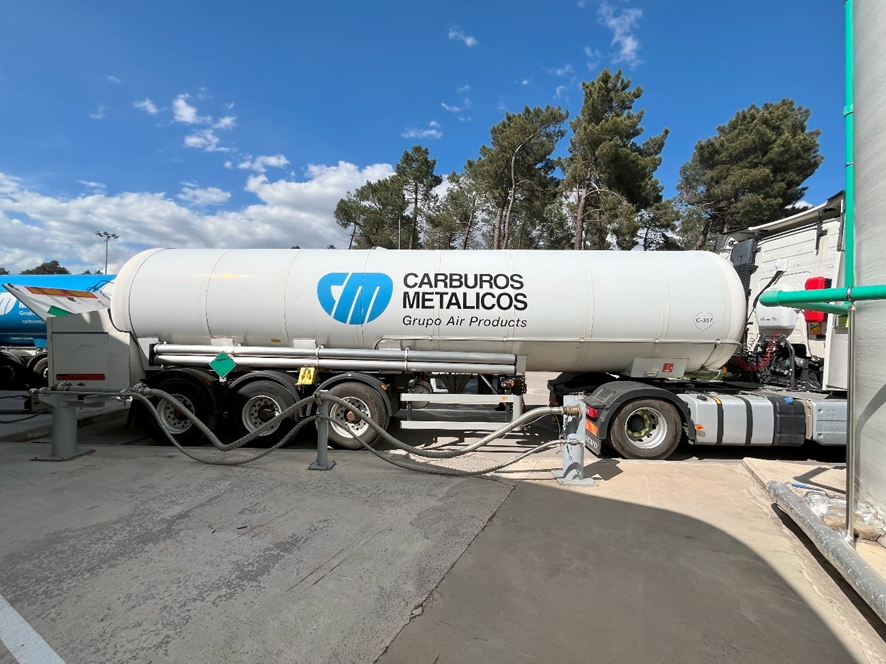
Ilustración 3 Camión cisterna para el transporte por carretera de dióxido de carbono licuado.
Consumos térmicos
Para el caso de la tecnología de captura con disolventes químicos, se requiere adicionalmente de un aporte de energía térmica, generalmente mediante el empleo de vapor a baja presión entre 3 – 5 barg. Esto es importante tenerlo en cuenta a la hora de plantear un proyecto de captura tanto por el hecho de que es necesario contar con un suministro estable de vapor, como por la necesidad de que ese vapor sea de origen renovable.
Dado que por cada tonelada de dióxido de carbono capturado se requieren entre 1 – 2 toneladas de vapor de baja presión (0,6 – 1,2 MWh/t CO2 de energía térmica), en numerosas ocasiones, aunque el proyecto se ubique en un entorno industrial existente, no siempre se cuenta con calor residual suficiente como para cubrir la demanda térmica del proceso.
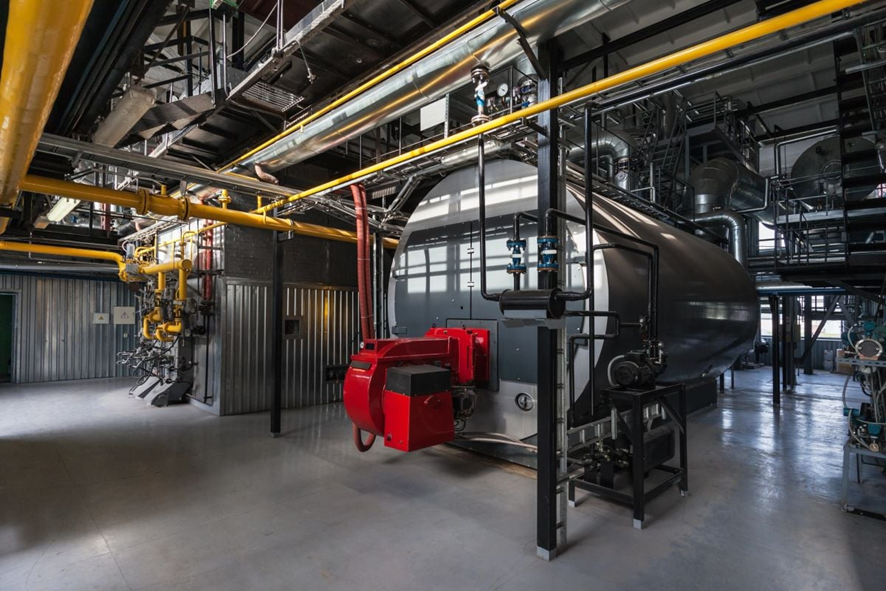
Ilustración 4. Caldera industrial de generación de vapor. Fuente: (CoolPlanet, 2023)
Por este motivo, se deben considerar desde el inicio posibles integraciones energéticas entre la planta de captura y otros procesos como podría ser la producción de RFNBOs como el metanol renovable o el SAF (en caso de que la planta de captura se acople a una planta de obtención combustible), o el calor residual de los gases de escape de los que se va a capturar el CO2, ya que permiten reducir la necesidad de importar calor de otras fuentes. Este punto de las demandas energéticas es uno de los principales aspectos que deben considerarse en la integración de plantas de captura y de combustibles sostenibles, pues especialmente la producción de SAF es un proceso exotérmico que genera grandes cantidades de vapor susceptibles de ser usadas como aporte energético en la desorción del CO2.
Como resultado de estas elevadas demandas térmicas, es muy común requerir de sistemas auxiliares de generación de vapor para cubrir la demanda de la etapa de desorción del dióxido de carbono. Entre las soluciones más empleadas destacan las calderas convencionales de generación de vapor. Sin embargo, estas calderas deberán emplear preferiblemente combustibles renovables, pues de lo contrario contribuirían a aumentar la intensidad de carbono del CO2 y de los productos derivados que se obtengan. Una solución que cada vez está ganando más fuerza recientemente es la de emplear calderas eléctricas o, en su defecto, sustituir los circuitos de vapor por sistemas de fluidos térmicos a alta temperatura que permitan una electrificación directa del aporte de calor. Estas tecnologías ofrecen la ventaja de que, al ser alimentadas por energías renovables, el calor aportado al proceso no contribuye a aumentar las emisiones de GEI.
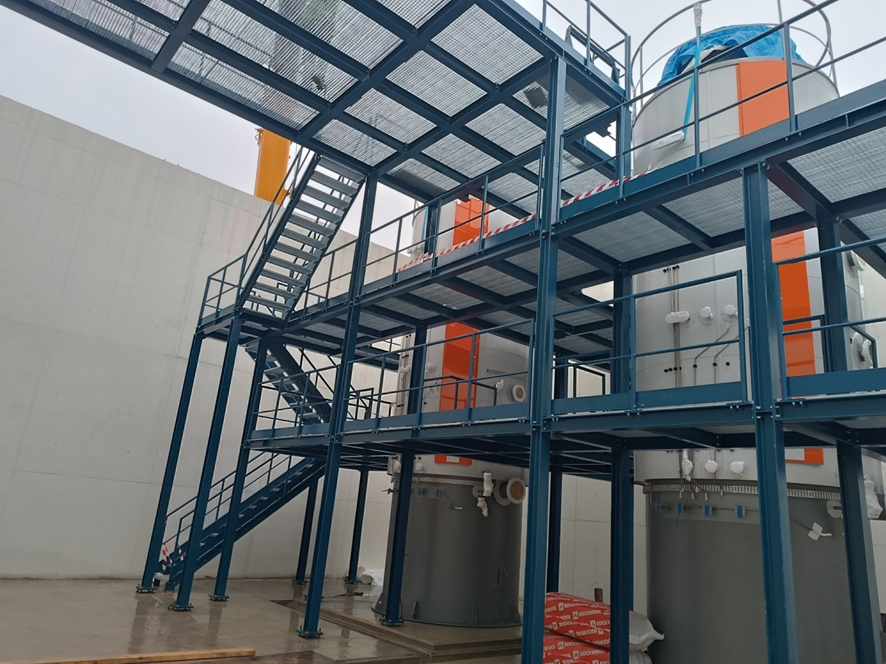
Ilustración 5. Calderas eléctricas desarrolladas por AITESA. Fuente: (AITESA, 2024)
Consumos generales
A modo de referencia, los consumos genéricos para una planta de captura de 100.000 t CO2/año basada en tecnología de aminas son los siguientes:
Tabla 1. Consumos genéricos de una planta de captura con capacidad para 100.000 t CO2/año.
Parámetro | Valor | Unidades |
Capacidad de captura | 100.000 | t CO2/año |
Potencia eléctrica | 0,7 | MWe |
Potencia térmica | 11,3 | MWt |
Consumo de vapor | 18,75 | t/h |
Demanda de refrigeración | 16,4 | MWt |
Integración de la captura en plantas de combustibles RFNBOs y compatibilidad con procesos existentes
A la hora de plantear un proyecto de captura de carbono en instalaciones industriales existentes, se deben tener en cuenta todos los factores asociados tanto a la propia planta de captura como al entorno industrial en el que se vaya a instalar. De esta manera, para un diseño apropiado que asegure que la captura es eficiente y competitiva, se debe comprobar la compatibilidad de capturar el CO2 con el proceso existente en la actualidad.
Por ello, se debe analizar en profundidad la fuente de emisión del dióxido de carbono y el destino actual/uso del gas de escape, pues generalmente o se dirigen a sistemas de tratamiento de gases para eliminación de contaminantes antes de ser venteados a la atmósfera por una chimenea, o se emplean en procesos de integración energética dentro del proceso de producción.
En el caso de que el gas de escape se emplee para integración energética, tenemos situaciones coma las de las industrias que aprovechan el calor residual de las emisiones de sus unidades de combustión para procesos de secado. En este ámbito, para producirse el secado de la materia prima con el gas de escape, tiene lugar un fenómeno de dilución con aire atmosférico que hace que la concentración de CO2 disminuya y, por lo tanto, se vuelva más complejo el proceso de captura.
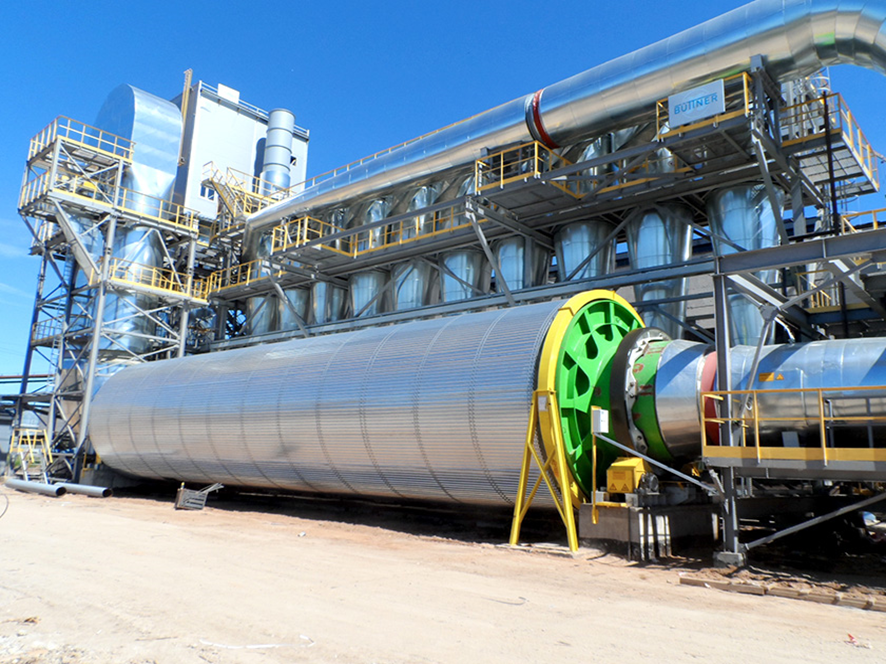
Ilustración 6. Secadero industrial rotativo. Fuente: (Buttner, 2024)
En estos casos, una solución válida puede ser la instalación de un intercambiador de calor aire-gas que permita calentar aire atmosférico con el calor residual del gas de escape de forma indirecta, evitando así es dilución del CO2 al mismo tiempo que se logra secar la materia prima. Esta solución aumenta el CAPEX de la planta de captura por la inversión asociada al recuperador de calor, pero permite mantener una concentración de dióxido adecuada para su captura mediante, por ejemplo, disolventes basados en aminas.
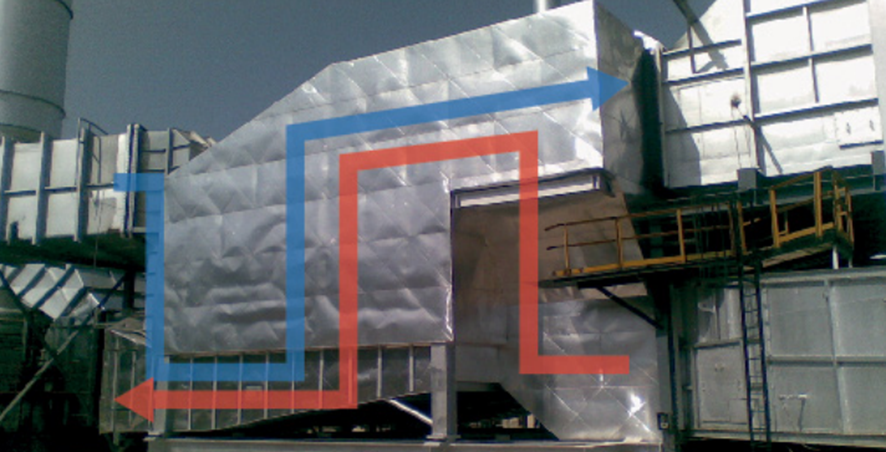
Ilustración 7. Unidad de recuperación de calor de gases de Kelvion Thermal Solutions. Fuente: (Kelvion Thermal Solutions, 2024).
Al mismo tiempo, debido a que los procesos de pretratamiento del gas de escape requieren de cierta temperatura para operar correctamente, es necesario asegurar que la integración energética realizada no hace que la temperatura del gas de escape cae a menos de 200 – 250 ºC antes de entrar a la sección de eliminación de impurezas, pues estos valores de temperatura son los límites en los que los sistemas de eliminación de compuestos como los de azufre operan de forma óptima.
Por todos estos motivos, durante la etapa de diseño de una planta de captura, no sólo importa lo que abarca el proceso de captura en sí, sino también los procesos ya existentes e incluso las posibles plantas colocalizadas de producción de combustibles derivados del CO2, pues la integración de procesos puede llegar a suponer mejoras significativas que lleven a reducciones de costes y una operación más eficiente.
No olvides que desde AtlantHy trabajamos diariamente en proyectos de captura de CO2 con grandes éxitos en nuestra trayectoria. Tanto a nivel de consultoría e ingeniería como de tramitación de ayudas.
¡No dudes en contactarnos para hacer despegar tu proyecto de captura de carbono!
Si te ha gustado este artículo, permanece atento para seguir aprendiendo en la tercera parte, donde hablaremos sobre diversos aprendizajes en el planteamiento de este tipo de plantas… ¡Síguenos en AtlantHy Academy!
Referencias
AITESA. (2024). Calderas eléctricas de alta tensión de electrodos. Obtenido de https://aitesa.es/caldera-electrica-industrial-alto-voltaje/
Buttner. (2024). Rotary drum dryers for biomass products. Obtenido de https://www.buettner-energy-dryer.com/en/industrial-dryer-systems/rotary-drum-dryers/
CoolPlanet. (2023). Maximising Boiler Efficiency: Reducing Costs. Obtenido de https://www.coolplanet.io/blog/articles/boiler-efficiency-and-decarbonisation
Global CCUS Institute. (2021). Technology Readiness and Costs of CCS.
Kelvion Thermal Solutions. (2024). Rekuluvo: Combustion Air Preheater. Obtenido de https://www.kts.kelvion.com/_files/ugd/3c9275_1d724936c7794f5ca51ed8a7fdf1ec82.pdf
Perspective. Frontiers in Energy Research.